Continuous Wet Systems
Continuous wet systems are particularly well suited for by-products with low fat content and high humidity, such as the waste from slaughtering chickens, offal and fish waste.
This system can separate fat and water mechanically at low temperatures, and for chicken waste, allow the user to obtain a higher quality chicken fat.
In fact, after a rapid heating step, the product goes through a twin screw press that separates the liquids from the solid parts.
The liquid part then passes through a decanter, and through separators that divide it into three parts – fat, water and solid.
The solid that comes out of the twin screw press and the powder are processed in the dryer, which produces dehydrated meal.
Water discharged by the separators is introduced into the concentrators that evaporate it and increase the concentration of the solid dissolved in it, which is then sent to the dryer.
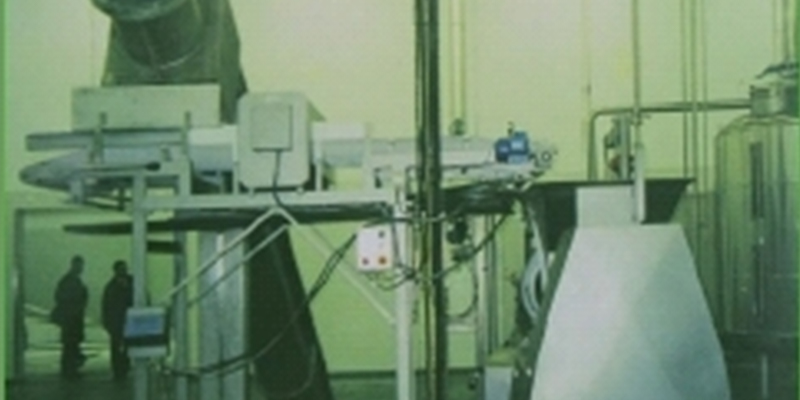
Metal Detector
Eliminates metallic objects that may be contained in the raw materials, thus preventing damage to machinery.
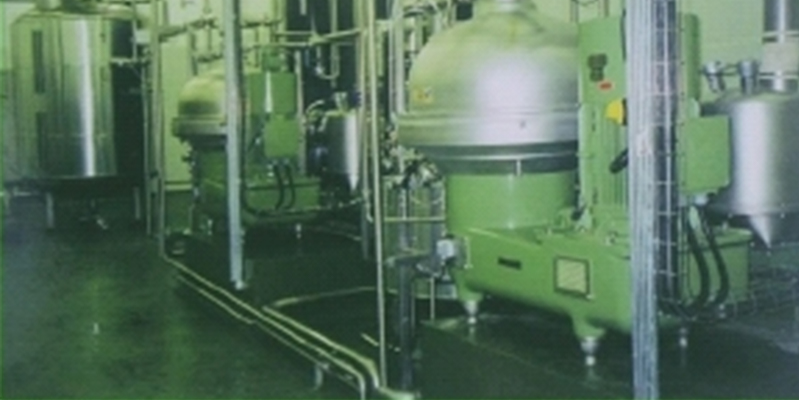
Centrifugal machines
These machines separate the water and fat from the twin screw press.
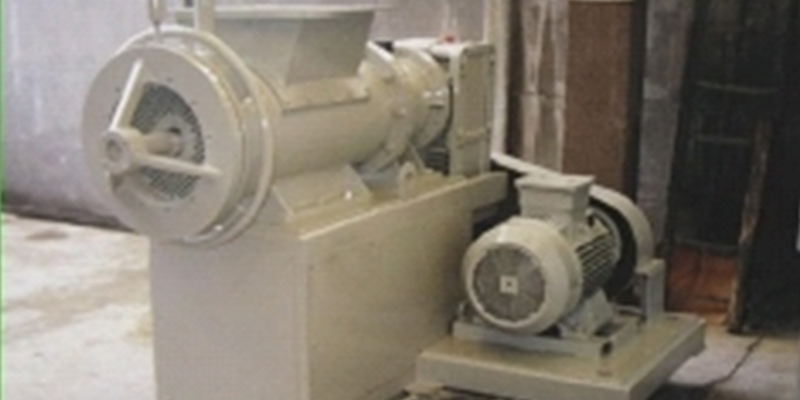
Mincer
Grinds raw materials into tiny pieces to allow more effective preheating and perfect pressing. Strong worm screw conveyor with anti-wear treatment. Interchangeable grids to produce various grain sizes. Complete with hoist to replace the grid.
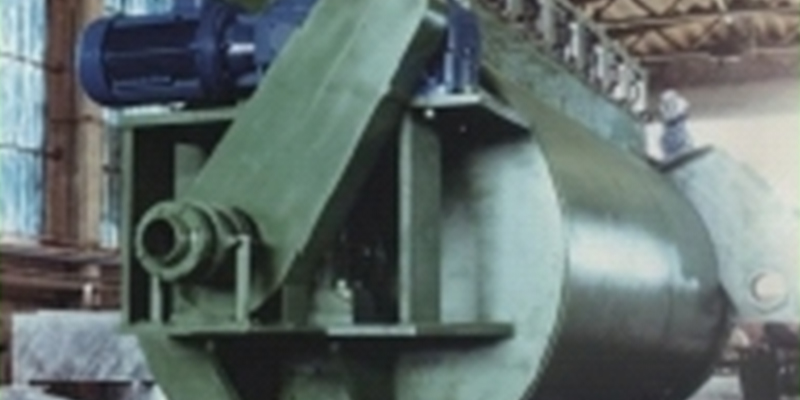
Preheater
This is composed of a cylindrical body with a horizontal axis. The internal shaft is composed of a central axis onto which is fixed a series of heating disks with relevant blades for feeding and discharging the product. It can be heated with steam, hot water or with diathermic oil. Made in carbon or stainless steel.
Twin screw press
This machine separates liquids from solids. It uses a mechanical process to efficiently separate 70% of the water and 90% of the fat in the material. Strainer cage with cover and mesh in carbon steel or stainless steel. Shafts with anti-wear coating in stellite. Parallel axes gear box.
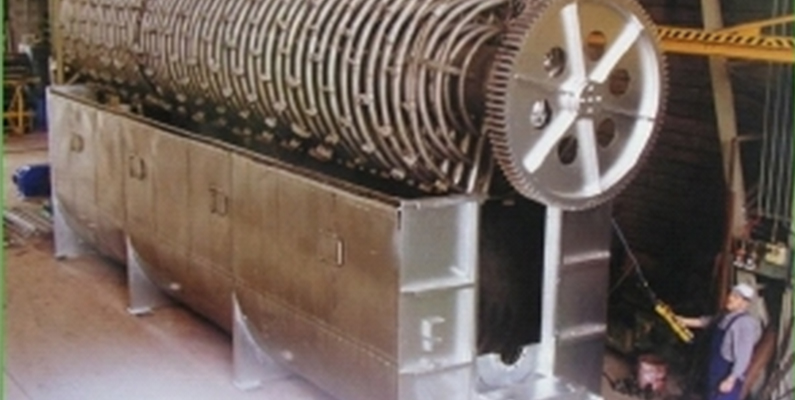
Dryer
The machine has a U-shaped body. The internal shaft has a central axis with a series of concentric spiral tubes, each with a blade for pushing and discharging the product. These tubes serve to heat the product. Heated with steam at a pressure of 10 bar. Built in carbon steel or stainless steel.